We are a leading manufacturer of machines and systems for processing insulation materials and construction elements.
We design, build and automate machinery and systems for the insulation and construction elements industry. We link proven Kraft Group systems, such as feeding systems, saws, stacking systems and the comprehensive handling components, for example, with our laminating, drilling and edge processing machines to create a high-performance all-in-one solution.
Our many years of development expertise have led to the development of high-performance, customized special solutions with higher throughput and efficiency.
Innovative software solutions round off the extensive range of services.
Everything from a single source – from the Kraft Group – for you
Insulation materials
We are a leading manufacturer of machines and systems for processing insulation materials.
Polyurethane (PUR/PIR) sandwich elements with metallic and flexible protective layers, XPS, EPS and mineral wool, for example, are processed for insulation materials. At a time when increasingly stringent requirements are being placed on thermal insulation to save energy and protect the environment, these products have become an essential and cutting-edge material.
Thanks to our expertise, decades of experience and innovations, the Kraft Group can offer the perfect solution for every application (conveying, sawing, trimming, profiling, machining, storing). Individual and customer-specific special solutions round off our range of services.
Our automation team develops efficient controls based on Beckhoff or Siemens devices according to the specific customer requirements. Tailor-made concepts allow a significant increase in productivity and quality for the future.
Master computer systems ensure a process-optimized data exchange between your ERP system and the Kraft Group machinery and system controls.
Modular, individual machines and systems for your applications
- Continuous systems for the production of sandwich elements and insulation panels with core made of rigid polyurethane foam (PUR/PIR)
- Trimming, profiling, sawing and dividing, gluing and laminating of polyurethane, EPS, XPS rigid foam panels or foam glass panels as well as mineral wool materials
- Transporting, stacking, rotating, turning or storing a wide variety of products and materials
- Processing of panel-shaped composite materials consisting of various insulating materials with and without cover layers
Contact us. We will be happy to advise you.
Application example
Continuous production line for processing insulation panels with flexible facings on both sides and a core of rigid polyurethane foam (PUR/PIR)
The endless strand of the element supplied by the sandwich plate conveyor is divided into motherboards via diagonal saws and conveyed to the cooling and hardening section via roller and belt conveyors.
The cooling and hardening section, executed as a space-saving paternoster system (as option as horizontal cooling section), ensures consistent dimensions of the insulation panel, which is then forwarded for further processing.
The longitudinal edges are processed in the throughfeed via a longitudinal profiling device with tongue and groove, stepped rebate or smooth contour.
In the dividing saw, the motherboards are cut to preset, smaller formats where they are supplied to the cross profiling unit. The insulation panels can also be provided with tongue and groove, stepped rebate or smooth contour in the cross direction.
The processed insulation panels are transported to a collecting station by conveyors and are then aligned.
A stacking gantry assembles the insulation panels into packages. These packages pass through the shrink wrap tunnel and are packaged to match the customer's requirements.
A package stacker is used to stagger the packages crosswise, depending on the format, stack them up to a height of 2,400 mm and deliver them to the finished parts warehouse.
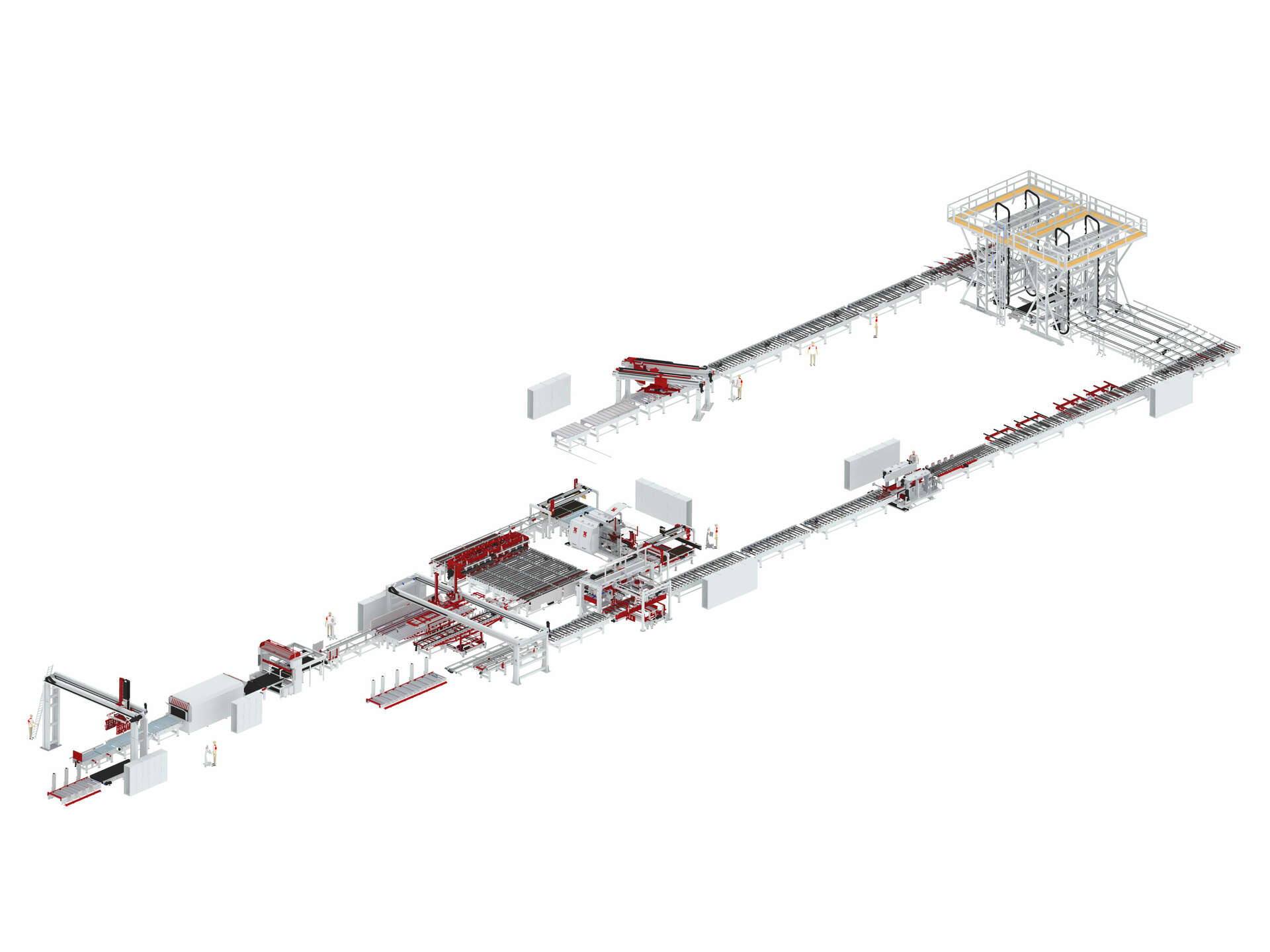
Stacking/Order picking
Roller conveyor
Gantry
Link chain conveyor
Packaging
Film packaging
Side sealing
Shrink wrap tunnel
Belt conveyor
Packaging
Collecting station
Gantry
Belt conveyor
Floor roller conveyor
Roller conveyor
Crosswise processing
Roller conveyor
Dividing saw
Angular transfer
Double-end tenoner
Belt conveyor
Turner 180°
Dividing area
Roller conveyor
Diagonal saw
Longitudinal machining
Angular transfer
Roller conveyor
Double-end tenoner
Cooling area
Angular transfer
Loading device
Horizontal cooling section/ paternoster system
Removal device
Toothed belt conveyor
Construction elements
We are a leading manufacturer of machines and systems for processing components.
Wood-based panels, solid wood, gypsum, fiber and cement materials, sectional door elements, formwork elements, multi-layer and acoustic panels, for example, are all processed for construction elements.
Thanks to our expertise, decades of experience and innovations, we can offer the perfect solution for every application. Individual and customer-specific special solutions round off the Kraft Group's range of services.
Our automation team develops efficient controls based on Beckhoff or Siemens devices according to the specific customer requirements. Tailor-made concepts allow a significant increase in productivity and quality for the future.
Master computer systems ensure a process-optimized data exchange between your ERP system and the Kraft Group machinery and system controls.
Modular, individual machines and systems for your applications
- Machining, among others, with double-end tenoners of plate-shaped materials, such as: Particleboard, MDF, HDF, OSB, plywood, mineral fiber, gypsum board, cement board and fiberboard as well as wall and ceiling panels, plastics and non-ferrous metals
- Handling components, such as transport, stacking, rotating, turning or storing
- Processing such as trimming, edge profiling, sawing and splitting
- Bonding, such as gluing and laminating for composite materials
- Drilling, setting rivet nuts, drawing in seals, mounting fittings and masking off surfaces
- Screwing, gluing, riveting or clinching different material combinations
- Deployment of industrial robots, e.g. for fully automatic clamping of corner joints for frame parts
- Customized designs
Contact us. We will be happy to advise you.
Application example
Production line for the processing components
The wood-based panels supplied by the tandem gantry are profiled on the longitudinal side with tongue and groove using a double-end tenoner. The workpieces are then cut or divided into different formats using a dividing saw.
Cross-machining is then performed by a second double-end tenoner. A linear gantry is used for the final destacking. A transfer carriage distributes the stacks to downstream roller conveyors.
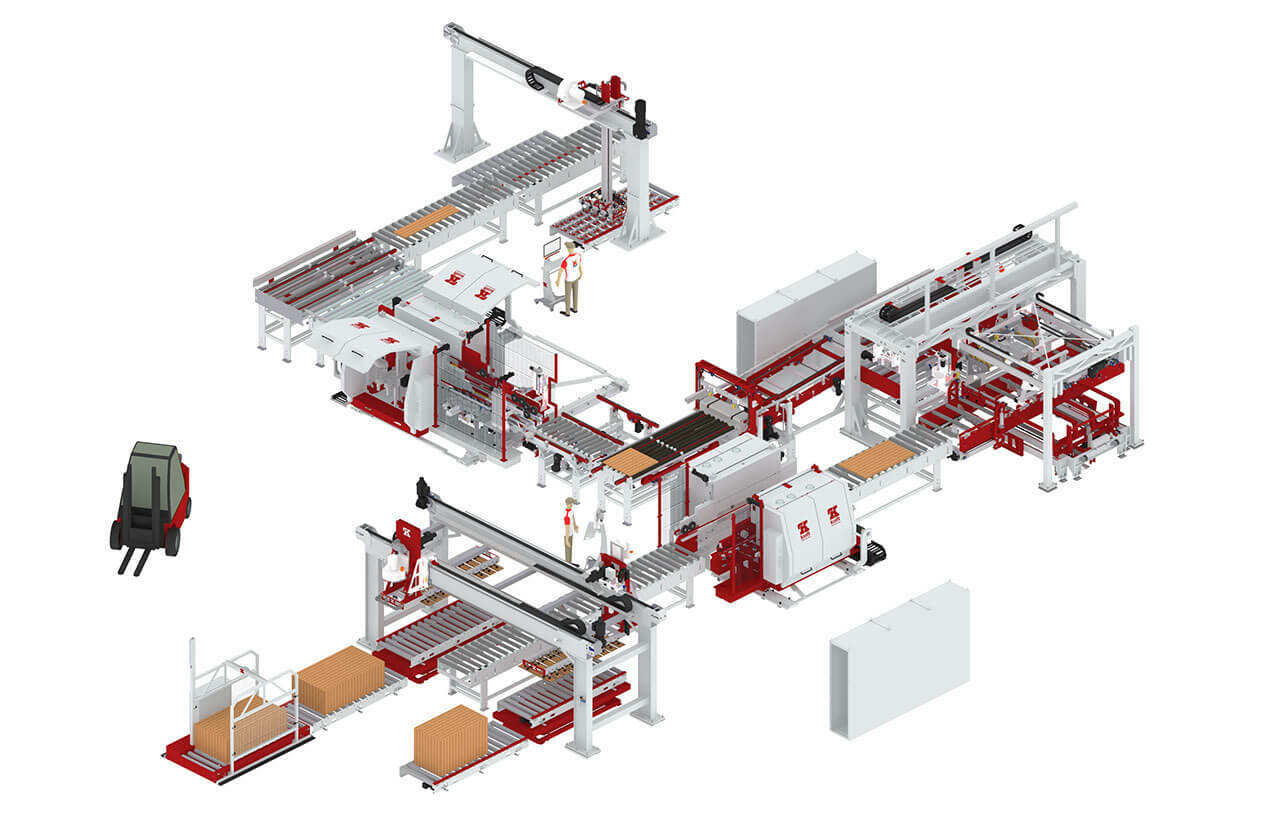
Loading
Cross transfer carriage
Floor roller conveyor
Scissor-type lifting table
Roller conveyor
Tandem gantry
Stacking/Order picking
Angular transfer
Roller conveyor
Floor roller conveyor
Gantry system
Crosswise processing
Transport unit
Double-end tenoner
Roller conveyor
Longitudinal machining
Double-end tenoner
Roller conveyor
Dividing
Dividing saw
Infeed conveyor
Angular transfer